
Optimising Bearing Parameters In a Cycloidal Drive with Planetary Input
All Blogs, Articles & PapersWe explore how bearing parameters in a robotics transmission can be optimised to improve the drive’s performance characteristics whilst maintaining component lifetimes.
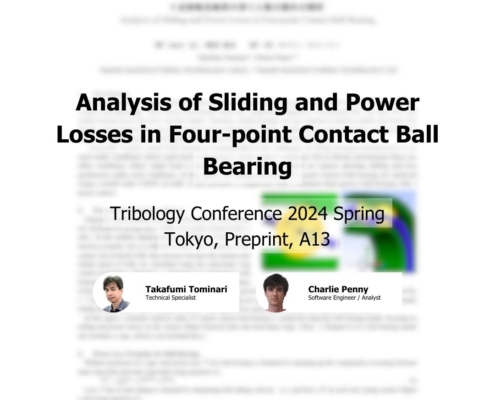
Analysis of Sliding and Power Losses in Four-point Contact Ball Bearing
All Blogs, Articles & PapersPaper written by Takafumi Tominari and Charlie Penny, presented at the Tribology Conference 2024 Spring Tokyo, Preprint, A13.
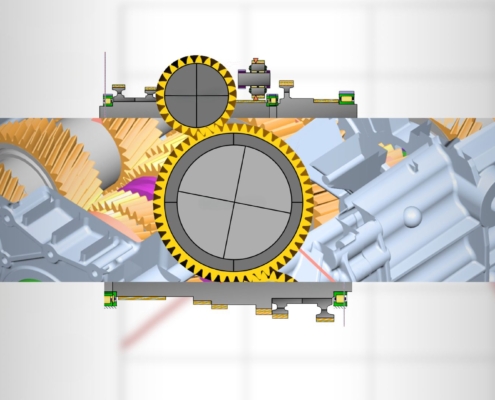
Predicting Unloaded Gear Rattle Using DRIVA
All Blogs, Articles & Papers, SoftwareSenior Research Engineer, Simon Terry, looks at unloaded gear rattle: why it occurs, how it relates to engine torsional vibrations and how MASTA’s DRIVA modules can be used to accurately model rattle in a vehicle on-road scenario.
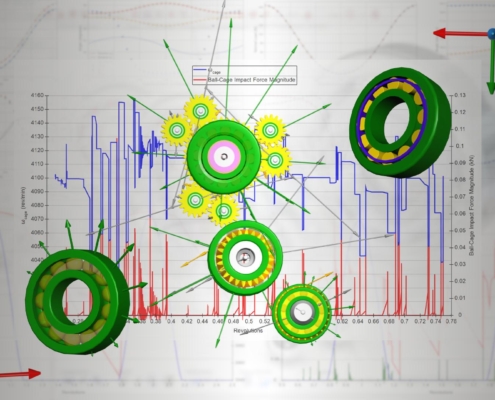
High-Speed Ball Bearings – Dynamic Models
All Blogs, Articles & Papers, SoftwareWe look at the dynamic modelling of ball bearings, and the benefits of this approach when analysing high-speed ball bearings.
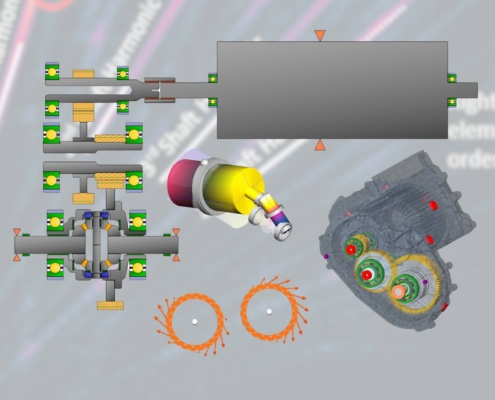
Predicting Spline Rumble
All Blogs, Articles & Papers, SoftwareWe look at how to predict rumble in a modern EV gearbox using MASTA, covering quasi-static analysis, a time stepping analysis and manufacturing errors to see how different errors contribute to rumble.
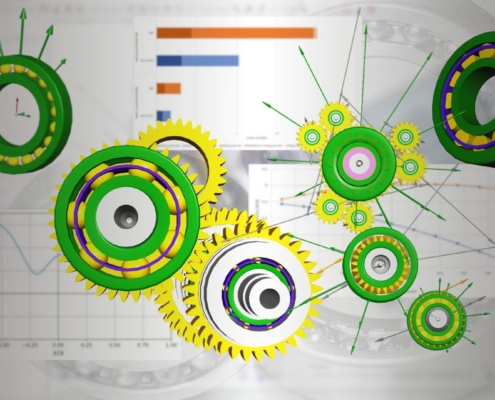
High-Speed Ball Bearings – Challenges and Analysis
All Blogs, Articles & PapersThis article explores and focusses on the behaviour of ball bearings at high speed, but much of it is also relevant to roller bearings.
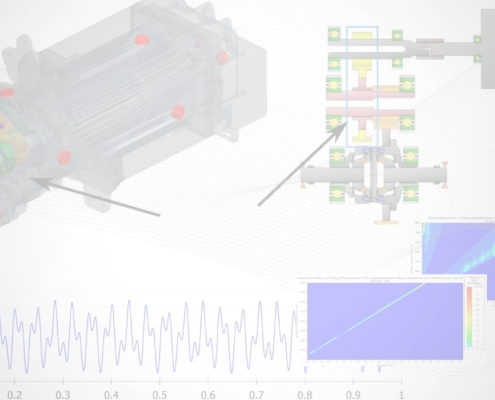
Sidebands In Gear Noise Due To Manufacturing Errors
All Blogs, Articles & PapersWe discuss how the automotive industry uses a high-fidelity MASTA analysis for NVH in electric vehicle powertrains.
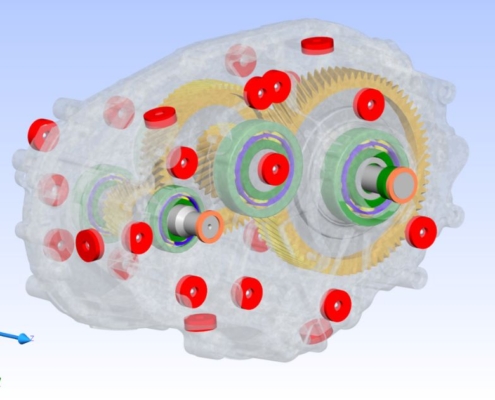
Modal Testing Validation Of An EV Gearbox Model – Part 3, Bearing Connection Methods
All Blogs, Articles & Papers, NewsPart 3 includes a full gearbox casing made of two separate halves bolted together and gearbox internals of gears, shafts and bearings.
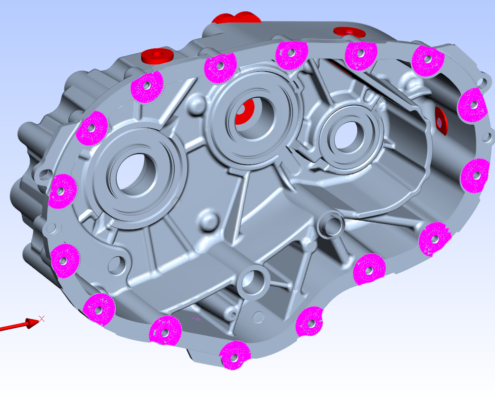
Modal Testing Validation Of An EV Gearbox Model – Part 2, Casing Bonding Methods
All Blogs, Articles & Papers, NewsPart 2 expands on this research by including a full gearbox casing made of two separate halves bolted together.
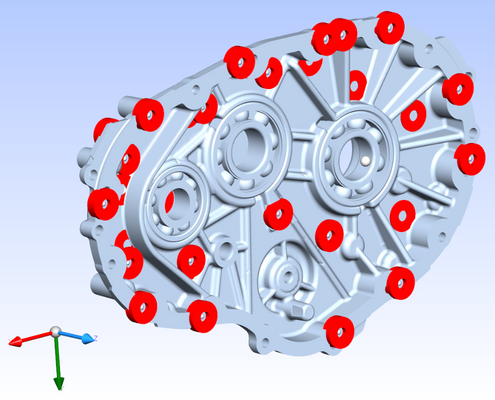
Modal Testing Validation Of An EV Gearbox Model – Part 1
All Blogs, Articles & Papers, NewsWe show you validation work of MASTA software against NVH modal test data on a single-speed, two-stage EV gearbox casing half.